Studio Visit: Rhythms of Daily Work
sections of my large drawing cut up and ready to be copied
Good afternoon friends, I hope you're enjoying your weekend so far!
When working on a large scale ceramic mosaic there’s a whole lot of process. I’ve had a Hawaiian landscape pool house mosaic in process for about 5 months now and there is still much work to do. In fact, in this last 7 weeks until the project is complete the intensity is ramping up.
I’m fully immersed in the cutting, glazing, firing, and assessing results on a daily basis and in this post I’m going to show you an average day -yesterday in fact - in the life of this project. If you want musical accompaniment while reading this, scroll to the bottom and then back up to continue.
In case you’re new to my blog or to this project and are interested in scanning some images to see what’s led to this point, here are a few recent posts showing the drawing phase, some clay cutting and some glazing
Each day work towards this mosaic represents 4-6 hours of my time and begins with a look at the kilns to see where they are in their cycles and what the results are.
Today I have a bisque in its slow “pre-heat” phase and 2 glaze firings that are cool and ready to unload. With a bisque firing I’m taking clay that is more or less dry to the touch and heating it to 1923 degrees F. This firing and cooling cycle is about 18 hours and once unloaded these tiles are ready for glaze.
Below are 2 kilns of tiles that have just undergone glaze firings to 1863 degrees F.
Usually when I open a kiln of glazed work, I'll loosely arrange the pieces together to get an idea of how it looks.
Although it mostly looks like a mess, it helps me enormously to see what I've glazed so far altogether or at least near the other parts.
Over time these seemingly incoherent parts will start to make more sense.
After checking the kilns and putting together glazed tiles I sometimes dive right into more glazing especially if whatever comes out of the kiln inspires the next steps, and today I wanted to put another coat of glaze on some of the tiles to darken the color.
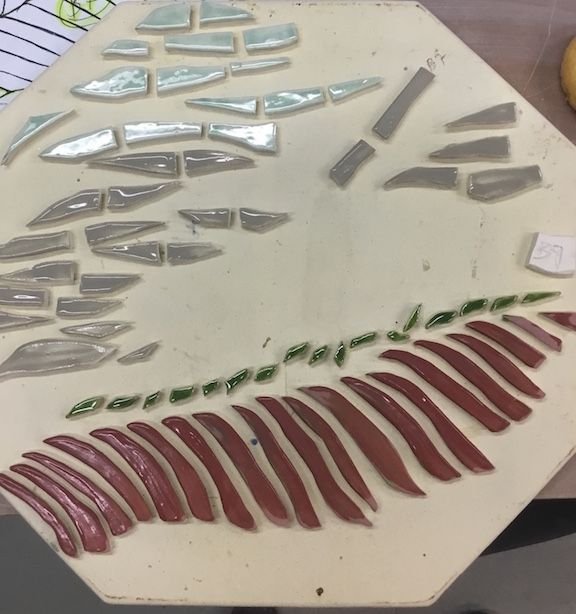
Projects like this one require my focused and undivided attention so I try to take care of other work and odds and ends in my studio first. Then later in the day I turn off the ringer on my phone so I can dive in to the cutting and glazing which require deep attention and focus in order to make good decisions and work efficiently.
Next I’m ready to begin cutting some tile:
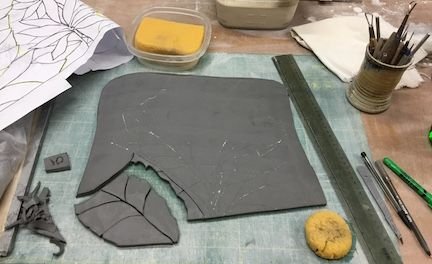
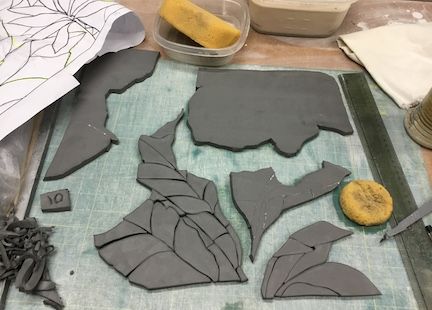
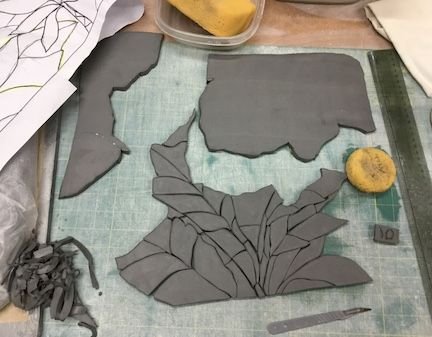
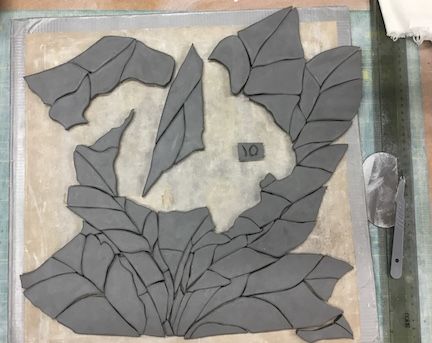
Most evenings I finish the session with packaging up clay slabs I rolled the night before in plastic and rolling some new ones, loading the kilns and cleaning up.
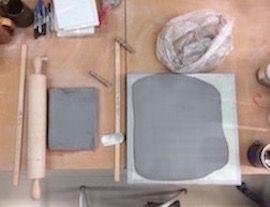
And I’m inspired by @opheliafu’s sharing of the music she listens to while working. I choose depending on what I'm doing and there are tasks during which I need silence and can't listen to anything. Yesterday when I could listen while I worked, I chose from the two audiobooks Mating in Captivity by Esther Perel, and The Alice Network by Kate Quinn and my music selections were Mutual Benefit (Love’s Crushing Diamond), Belle & Sebastian, Beulah, Grimes.
Here is (single song) Mutual Benefit's Advanced Falconry:
Have a great rest of your weekend and as always, thank you for your support of my blog, it's keeping me going!
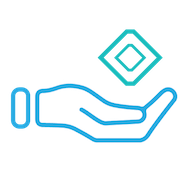
I would very much like to be able to do such a work. Learning the intricacies of this business and ..
But I'm not sure I can do it. You are an excellent artist and you have experience. I respect you The music you share is also wonderful!
thank you
thank you @artizm for your always supportive comments and upvotes, so glad you my posts are offering something!
Hello, I am so glad I found you here. Really nice work and loveful environment. I am painter and I´d like to start with ceramics also - to make my paintings as reliefs. Thanks for sharing! Following
Hi @jecminek, so glad to meet you as well! Just took a look at your blog and really like your work as well. I hope you do try ceramics and I'm happy to offer some tips if you have questions :-).
Your work is incredibly time-consuming and laborious. And at the same time, the result is so amazing that all efforts are worth it! I never cease to be excited about this process and your diligence and talent.
Thank you @anna-mi!
Wonderful post as always! very informative and a cool project! I've always been curious about the kiln temperatures and timing :) I don't know why, but it seems like such a mysterious process. I can't wait to begin working with clay and get a wheel and kiln!
Thanks @nickh725! I'll be selling some of my stuff before I move this summer so you may be able to get a few items at cut-rates to start your endeavors :-)
You'll have to let me know! that would be wonderful :) so the move is official now?!
Yes the move IS official even if I have a whole lot of trepidation about it! I'll be using my kilns up until the move but "pre-selling" ahead of time so people can just come and get them. If you're interested in these, let me know, the rest will be sold in a studio sale late in June.
Oh my. That looks like a really complex drawing @natureofbeing. Lovely to see some more of the tiles.
In those octagonal kilns, can you fire number of tiles at once? Are those slots for removable shelves?
Hi @gillianpearce! Those slots are for the electrical elements within the kiln. Those elements are coiled wires that run all the way around each section of the kiln. As they heat up, they heat the kiln and the tiles. I fire about 5-6 shelves of tile for each firing.
Thanks for following my process Gillian :-)
That must take a lot of firings then for a project the size of that swimming pool one! 😁
yes, MANY firings :-), over a hundred
Looking at what you have to do has me wow'd, looking at what you've done has me more wow'd. It is brilliant that you can clearly detail out your every step and progress, youre doing a awesome job
Otherwise you might make errors or worse cut yourself
I wish you more strength and Godspeed to complete the project
All the best
Thank you so much @mistakili!
Oh, I just love your work!
My friend gave me all of her mosaic-making equipment several years ago as her illness meant she just didn't have the energy to be able to make use of it. I have the same illness and so now the equipment has sat unused in the cupboard for several years as I haven't had the energy either.
However, now I am improving somewhat and I am facing the delicious prospect of maybe someday soon being able to spend some of my time playing and experimenting. It's a very exciting prospect!
I'm so glad I've found and followed you on here as your work is beeeeeyotiful.
Hello @sue-stevenson, fingers crossed for you to be in better and better health every day and soon to be able to do all the things you yearn to including mosaic-making! Thank you for your compliments :-)
Thank you for your well-wishes :)
Great idea to accompany the experience with some music. How come you print out 106% zooms, is it to enlarge some items compared to what you originally planed?
I think life is one big puzzle. Some see it, others don’t.
Lol - yes a big puzzle for sure :-)
I enlarge some parts to 103 and 106 depending on how much the piece will shrink in the kiln. Some shapes, some sizes shrink more than others. Thanks for this question @edouard.....I should have explained this and maybe this is a subject itself for a future post.
Yeah, I do think it would make a cool post. I would be curious to find out what shapes shrink more than others!
Oh wow, this is beautiful what you are doing! Are your customers requesting mosaics for inside or outside? I bet, you're spending a lot of time laying tiles for the pools of fancy mansions..
Hello @lisaliebeslust, I make a lot of exterior tile but mostly interior these days. Pool projects are really fun but I've only had 2 of those...hoping for more over time. And I only make the tile and don't install it. That's a different skill set for sure. Thanks for your support!
More fascinating process. And I'm with you on the concentration end of things, it's pretty much silence all the time during creativity. "Sshh Kitty, sshh". I think it comes from years of working in the quiet of the woods.
I do have a ? for you. It might be dumb, or answered already, but anyway....do you stamp a number on each piece, before you fire it? So you can keep track of where it goes? Or do you just memorize it, since you are SO familiar with it all from drawing to end result. Or is it a big jigsaw puzzle, till you get them on paper where they belong? Though a fun challenge, seems it would take WAY too much time to do it that way.
Just curious....seems like you end up with a LOT of pieces of tile that look very similar. And I think I know you can't put a piece of paper in the kiln, at 1900 and whatever degrees F.
Looks like it's coming along well. Can't wait to see the final photos one day soon. Cheers.
It's a very good question @ddschteinn! The short answer is that I don't number the pieces, but keep little sections together all the way through the process. The longer answer is - I cut a small area of tile and number this area. I mark the outlines of this section/area on the master drawing so I know all of parts in it as well as the outlines. That section once cut stays together with all its little pieces on the kiln shelf through the bisque firing and then when I glaze it, I look at the outlined area on the master drawing to make sure I know what each piece is - leaf or sky or whatever. It stays together through the glaze firing and at the end when it's time to assemble all of the pieces, either I am familiar enough with it, or I can again refer to the master drawing if I get confused. Does that make sense? I think you've just inspired a post heh heh ;-))
Thanks, that makes great sense. I can imagine without a very straightforward 'system', things could get a bit wonky. And the need to stay very well organized is very obvious. I better stay away from intense tile-art creation ( :
I think you also need a LOT of shelves...
I say, go for it, sounds like a great post idea. Glad I could tweak the idea curve a bit with my Curious D-isms.
Hahaha, yes a LOT of shelves indeed :-)
And I always enjoy your comments-conversations @ddschteinn, thank you for taking the time!