The Underlying Principle of Cavitation – A Menace in Hydraulic Machines
Hey friends, welcome here again.
Today promises to be another exciting article and I’m sure you will learn a few things in the field of hydraulics. It’s been a while since I wrote something in that area so today I have decided to present an interesting course to you – Cavitation.
Prolusion – The Boiling Phenomenon
Let me ask you a question
What is the boiling point (temperature) of water? 100 oC of course. Well, I suppose that’s too cheap to ask. However, is that completely correct? Perhaps the question was incomplete or maybe you were too hasty to conclude that the answer is 100 oC. Well, I won’t say you are wrong and neither will I say you are correct so instead of keeping you shrouded in any mystery (not really a mystery anyway) let’s explore the underlying principle here.
The principle behind boiling revolves around three parameters – vapour pressure, ambient pressure and temperature. Pressure is the amount of force applied over a unit area. When you stand on a surface with a single foot, you apply a pressure equal to your body-weight (a force) divided by the space occupied by your foot on such surface. Basically, pressure is simply a force, but taken over a defined area. Temperature on the other hand tells us how hot or cold an object is.
Furthermore, when we speak of boiling, we speak of a phenomenon whereby a liquid is at the verge of changing or changes into a gas. Thus it is a phase transition phenomenon. The common form of boiling is that of water which we do almost every day. Whether you need a hot water for direct use like taking a hot bath or to make coffee or you utilize it in other ways like cooking, you surely employ this phenomenon in one way or the other and at one point or the other.
Like I noted just earlier, three parameters are involved in the boiling phenomenon – vapour pressure, ambient pressure and temperature. I have given a general definition of pressure and as well as temperature and at this point it is essential to state clearly the vapour pressure and ambient pressure. Without going far, the ambient pressure is a pressure that must be defined with respect to a particular environment. The atmospheric pressure is an example, which is the pressure exerted by the surrounding air on us. Thus, simply put that ambient pressure is the pressure is exerted on a chosen matter by its enveloping environment.
We have often had the course to put some volume of water into a closed container on a stove and wait for it to boil. Without the addition of energy to the liquid, molecules constantly escape from the surface of the liquid, since evaporation occurs at all temperatures and at the same time these molecules re-enter the liquid, albeit this is not obvious to us. The amount of molecules leaving depends on the amount of energy which these molecules possess and this is a function of the temperature.
Under equilibrium condition, the vapour contained over the liquid surface exert a certain amount of pressure on the liquid surface corresponding to a given temperature. The pressure exerted by the vapour is called the vapour pressure (for obvious reasons).
As the temperature increases, the vapour pressure increases since more molecules will be liberated from the liquid surface. That is, every temperature has its corresponding vapour pressure. Thus as more heat is applied, more particles build up above the surface of the liquid and apply more pressure over this free surface. Thereby, further increasing the vapour pressure. At one point, the vapour pressure matches the ambient pressure and at that instant, boiling commences. The temperature at which this boiling occurs is called the Boiling point.
Hence, boiling is a phenomenon whereby the vapour pressure of a liquid matches the surrounding or ambient pressure. The vapour pressure of water at 100 oC is 1atm which equals the atmospheric pressure. Therefore, when water reaches 100 oC of temperature, it will boil under atmospheric condition. In a case where the pressure increases beyond 1 atm, water will not boil at 100 oC and this is because the vapour pressure of water at this temperature does not match the ambient temperature. Hence, we will need to supply more energy to increase the temperature in a bid to increase the vapour pressure to match whatever the ambient pressure is.
On the flipside, if the ambient pressure drops below 1 atm water will boil at a temperature below 100 oc. For instance, on the mountaintop, the atmospheric pressure there is lower than 1 atm and if we decide to boil water there probably during a picnic, expect that the water will boil sooner.
So back to my question once again. At what temperature does water boil? The answer in a loose sense is 100 oC. A better and more technical answer would be – 100 oC under atmospheric condition. Well, no one would blame you for saying the former as we are built to live under atmospheric conditions. But what about the machines? or more specifically in this course, the Hydraulic machines?
But first, what are hydraulic machines?
Hydraulic machines are type of machines that utilizes energy from a liquid to carry out mechanical work or vice versa. In this course, the discussion will be centered on pumps. Pumps are hydraulic machines that utilizes mechanical energy in a given form to impart energy to a given fluid. A very familiar example is the domestic water pump in our homes. Pumps do not function alone, they are used with piping systems, connected to their ends - inlet and outlet, that convey the working liquid to the pump and away from it.
Having said these, it is obvious that the aforementioned hydraulic machine handles liquid. A fact worthy of note is that during their operation, pressure variations occur within them. Thus, the liquid handled experiences different pressures at different points during its travel through these machines. In addition to this, such liquid could be handled at any temperature depending on the application involved. Hence, there is a tendency that the local pressure of the liquid matches or goes below its vapour pressure at its operating temperature and local boiling may occur, resulting in the formation of vapour bubbles in the bulk of the liquid. It is noteworthy that any dissolved gas at such location will also be liberated. This phenomenon is known as cavitation.
Let’s explore this phenomenon further

Cavitation and Pumps
As noted earlier, there occurs variation of pressure in pumps. There is a tendency that regions of low pressure exist and if such pressure at this local region is lower than the vapour pressure of the liquid at its operating temperature, localized boiling will occur. Consequently, vapour bubbles will be formed in this region. When such bubbles are swept to regions of higher pressure, implosion occurs.
An explosion is a common damage that sends waves outward. Implosion as in this case occurs in the reverse, that is, the waves travel inward. You can view this as compressing an inflated balloon without allowing it to swell in any direction. Surely, a collapse, that is an inward damage rather than an outward one will occur. When such implosion occurs near solid boundaries - the interior wall of the pump, in this case, serious damage may result as the imploding bubbles will cause a substantial amount of force to be exerted on the walls of the pump and this can result in erosion of metal surfaces.
So, where can we have low pressure in pumps?
The purpose of a pump is to increase the hydraulic energy of a fluid by imparting some energy to it. This imparts is carried out by a pumping element depending on the kind of pump utilized. Impellers, screws, diaphragms, gears, lobes are different pumping element that is utilized. The implication of this is that upon leaving the pump, the fluid will have more energy or pressure at the exit. We can thus easily conclude that the pressure at the inlet of the pump will be the lowest in the pump. The inlet and outlet of the pump are called suction and discharge respectively. The suction as said is associated with low pressure and the discharge handles higher pressure.
Having said this, it is obvious that the onset of cavitation in a pump is most likely at the suction. If the pressure at the suction of the pump is lower than that of the vapour pressure of the liquid handled at its operating temperature, cavitation sets in. The bubbles formed will then travel along in the pump to regions of higher pressure where they implode on any solid boundary in the vicinity of the implosion, such as the pump element or the walls of the pump interior, and causing severe damage of this internal components. The implosion of the bubbles results in pressure waves of high intensity that could be up to about 4000 atm and a local rise in temperature of about 800 oC.
Cavitation has varying effects in pumps ranging from fluctuating flow at the discharge, erratic vibration, noise, erosion of pump parts, overheated pump casing and so on.
The prevention of cavitation follows from its underlying principle, thus, ensuring that the suction pressure of the pump is always greater than the vapour pressure of the liquid at the operating temperature will keep cavitation at bay. For instance, to prevent cavitation in a pump handling water at 100 oC, since we know that the vapour pressure of water at this temperature is 1 atm, we must keep the suction pressure of such pump just above this value. Although this is in theory as in actual sense, cavitation can occur when there isn’t sufficient margin between the vapour pressure and the ambient pressure.
If Ps is the pressure at the suction of the pump and Pvp is the vapour pressure of the working liquid at the operating temperature. Then from a theoretical outlook, to prevent cavitation, the suction pressure must be greater than the vapour pressure.
That is, Ps > Pvp for cavitation to be kept at bay.
If we take the difference of these two pressures, say: P = Ps - Pvp, the P is the pressure available to ensure cavitation does not occur. These pressures we speak of can be taken as a pressure equivalent to the static pressure a column of liquid will apply above a certain datum (reference point). Generally, static pressure is given by P = pgH, where p is the density of the liquid, g is the gravitational acceleration and H is the height of the liquid measured above datum often called the head. If we make H the subject, then:
H = P/pg
Recall I noted that P is the pressure available to ensure cavitation does not occur. Hence, since H is the Head corresponding to Pressure P, H is thus the Head above which the vapour pressure of the liquid below which cavitation occur. This Head is what is called the Net Positive Suction Head (NPSH). The higher the NPSH available at the pump suction, the lesser the likelihood of cavitation. To do this, appropriate design and installation of the pump must be carried out such that the NPSH can be kept at an optimum value to prevent cavitation.

Closing
In theory, to prevent the occurrence of cavitation, NPSH must be greater than zero. However, as we all know, theoretical conditions do not hold true completely in reality. The theory assumes that there is no flaw and subsequent deterioration in the system under consideration as such holds firm on its established ground.
In reality, there are flaws and there will be subsequent deterioration in the system and in this case considered it will revolve around the pump and the piping system. For instance the pumping element may be malfunctioning or there could be clogging in the piping system. In such cases, the affected part will have to be repaired or replaced and as such does not involve the direct manipulation of the NPSH. In fact, this is most of the cases in reality.
In all, I believe you have been able to understand the underlying principle of boiling, how the same principle applies to cavitation and also how cavitation can be avoided.
Finally, the title points out cavitation as a phenomenon in hydraulic machines and you would want to believe that the scope of cavitation within this area. However, it is worthy of note that cavitation can occur in any hydraulic system such as turbines, bearings, valve, engines and so on, as long as there exist pressure variation in such system.
Thanks for being here. Till next time, keep steeming.

Reference
- Douglas, J. F., Gasiorek, J. M., Swaffield, J. A. and Jack, L. B. (2005). Fluid Mechanics (Fifth Edition). Pearson Education Limited.
- Kothandaraman, C.P and Rudramoorthy, R. Fluid Mechanics and Machinery (Second Edition)
- Vapour pressure
- Cavitation
- What is Pump Cavitation and How to Prevent it?
If you write STEM (Science, Technology, Engineering, and Mathematics) related posts, consider joining #steemSTEM on steemit chat or discord here. If you are from Nigeria, you may want to include the #stemng tag in your post. You can visit this blog by @stemng for more details.
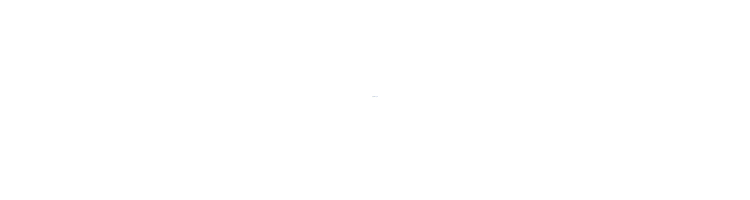
You can also join us at Promo-Mentors, to improve your blogging skills. Join our discord channel and meet awesome mentors who are willing and ready to shape your writing skills.
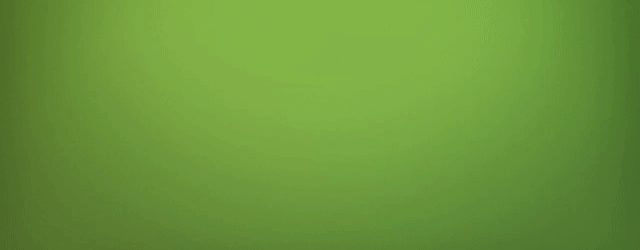
I only knew the basics. It was good to learn the details of it.
I'm glad you did.
I got schooled this time again. Your blog has always been a place to learn. The process of cavitation nicely analysed.
Kudos @temitayo-pelumi
Always nice to have you man. Your feedback is always an inspiration to me. Thanks for being here again.
Hello! I find your post valuable for the wafrica community! Thanks for the great post! @wafrica is now following you! ALWAYs follow @wafrica and use the wafrica tag!
I definitely can't forget about NPSH. I crammed that shii in fluid machinery. Now that I have left school, I sort of miss these kinda stuffs, cavity, NPSH, scale effect and the likes.
Thanks for bringing back good memories.
Yeah, the good old days. I actually thought I wouldn't miss them, but now I do.
Thanks pal. You have always been a support.
You are most welcome bro. You deserve it.
This is some deep engineering stuff. With my own little understanding, this is good.
Your writing ability captivates the audience. Beyond me!
I read about cavitation back then in my final undergraduate days didn't knew what they were exactly all i needed to do was store the definition in my head even though i don't know exactly what they are. But after reading this i can write as much on cavitation than i did in that exam. Good job
Those days one had to deal with pressure from different angles. It doesn't really give one much time to get to the root of many phenomenon. I'm glad I could shed light on this.
Thanks for stopping by.
yea, you were right tho...it was a good read
Interesting read as usual. I only had the literal understanding of cavitation. Thank you for the enlightenment.
Kudos bro.
It's always a pleasure having you here. I'm glad I could impart you.
Congratulations! Your post has been selected as a daily Steemit truffle! It is listed on rank 20 of all contributions awarded today. You can find the TOP DAILY TRUFFLE PICKS HERE.
I upvoted your contribution because to my mind your post is at least 17 SBD worth and should receive 107 votes. It's now up to the lovely Steemit community to make this come true.
I am
TrufflePig
, an Artificial Intelligence Bot that helps minnows and content curators using Machine Learning. If you are curious how I select content, you can find an explanation here!Have a nice day and sincerely yours,
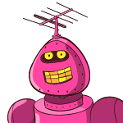
TrufflePig
Hi @temitayo-pelumi!
Your post was upvoted by utopian.io in cooperation with steemstem - supporting knowledge, innovation and technological advancement on the Steem Blockchain.
Contribute to Open Source with utopian.io
Learn how to contribute on our website and join the new open source economy.
Want to chat? Join the Utopian Community on Discord https://discord.gg/h52nFrV
I'm really grateful for your support for SteemSTEM. I hope the bot handler read this, sincerely I am.
Well done utopian-io.
Ara Oko...It is automated!..Be replying bot
I said the "handler"... Village boy.
Changes nothing..Be reply bot kiri..
How many posts handler wan see..Radarada
Bros, is it your reply?
Cavitation! A danger to machines like friction due to lack of lubricants....It is nice to get a clearer view with enough analogy at our disposal here. Well done once again, you are always giving us well thought and presented posts.
So, when there's low flow from taps even with a full tank, I believe it is because of the presence of an airlock..Is it a case of cavitation that led to it? I am not sure I asked the right question. But, I believe you can help me out.
Thanks
Awesome post mate
Airlock certainly cause reduced flow and that's due to the blockage of flow path by gases, air mostly. Gases could get into the system in a number of ways including from dissolved gases getting out of solution probably at higher temperatures. So, cavitation is a possibility in airlocks.
Thanks for being here man.
Nice! Been trying to find clarifications.....Thanks for the prompt reply!